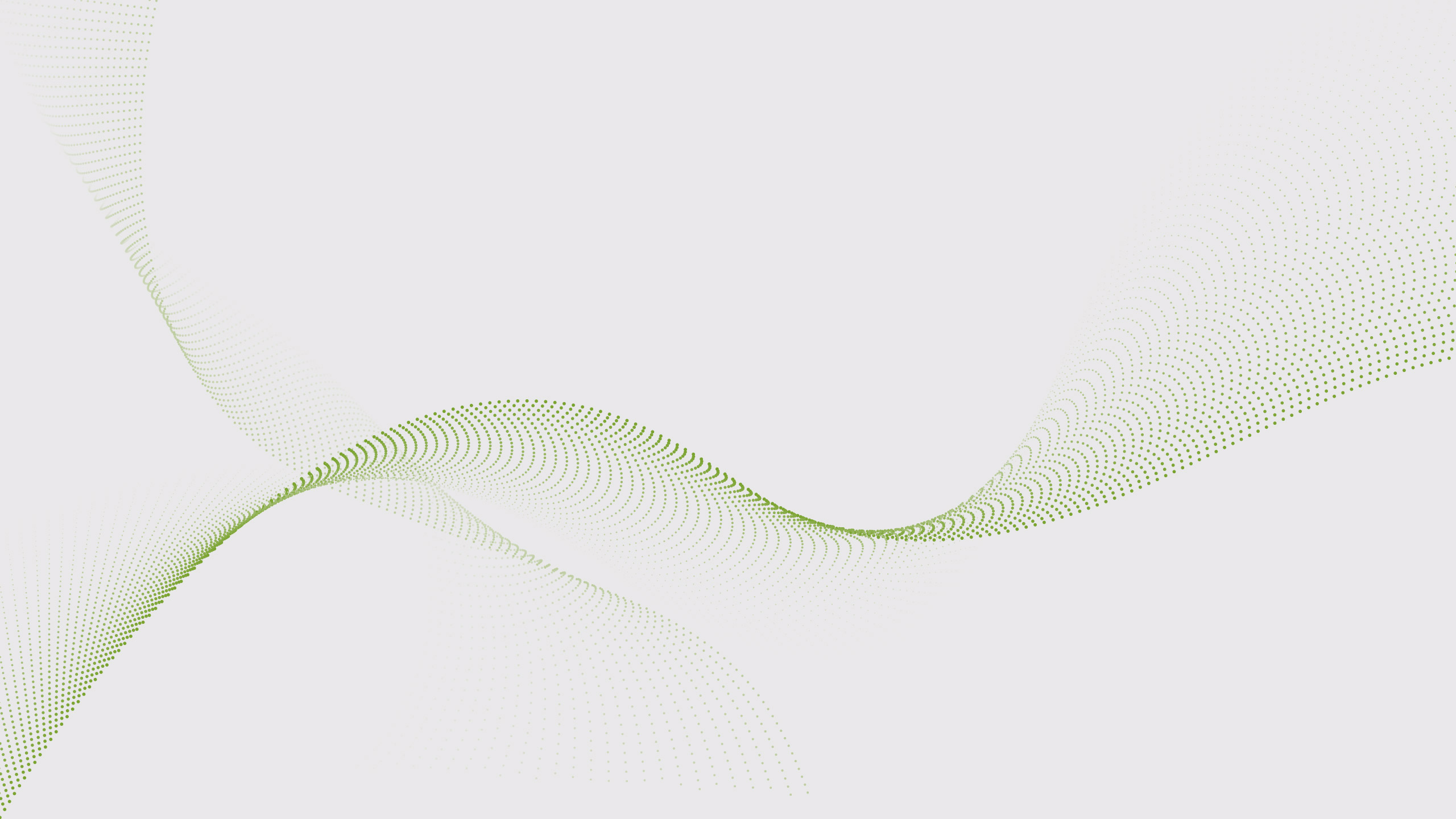
How to kick start your OT security with ZTNA
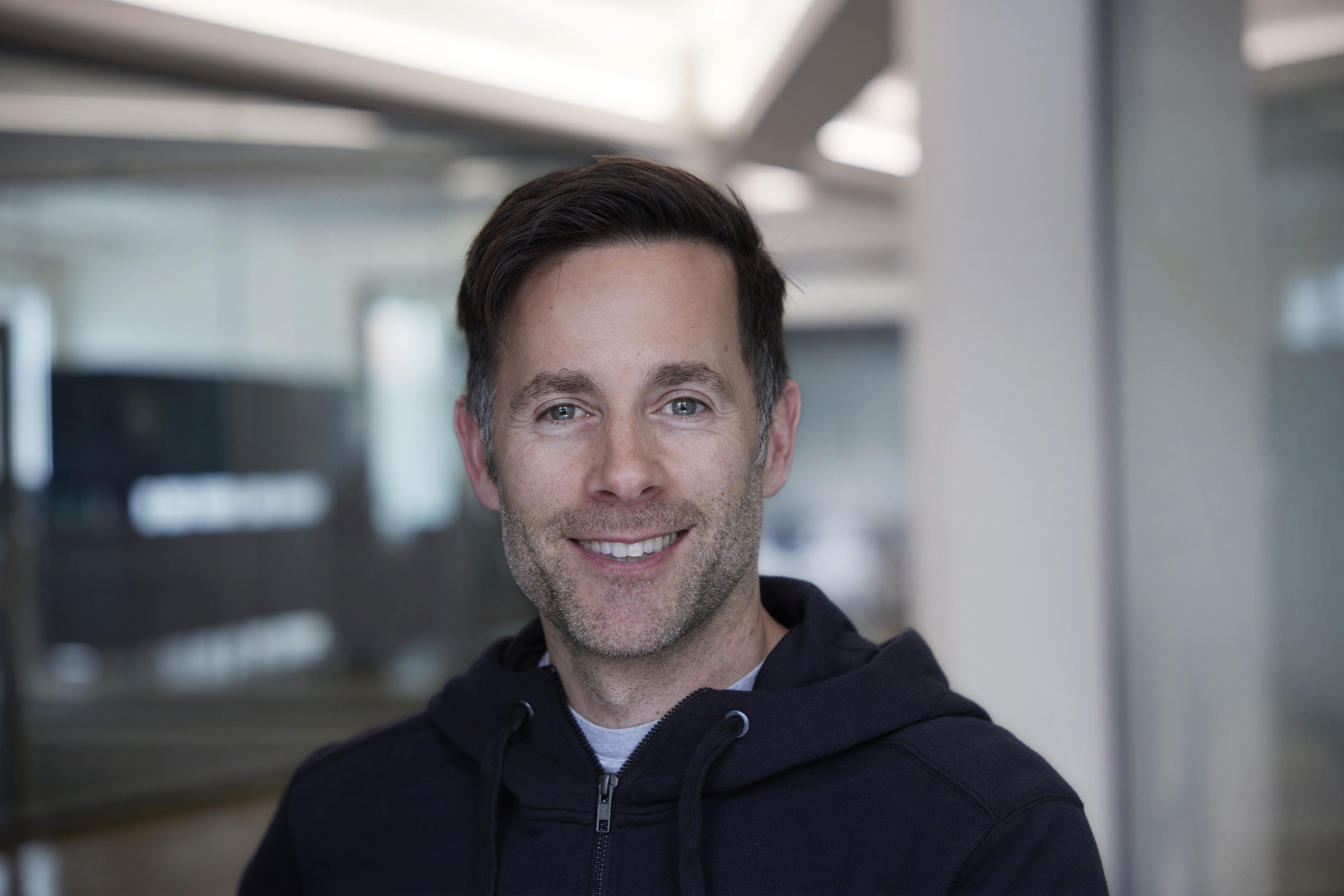
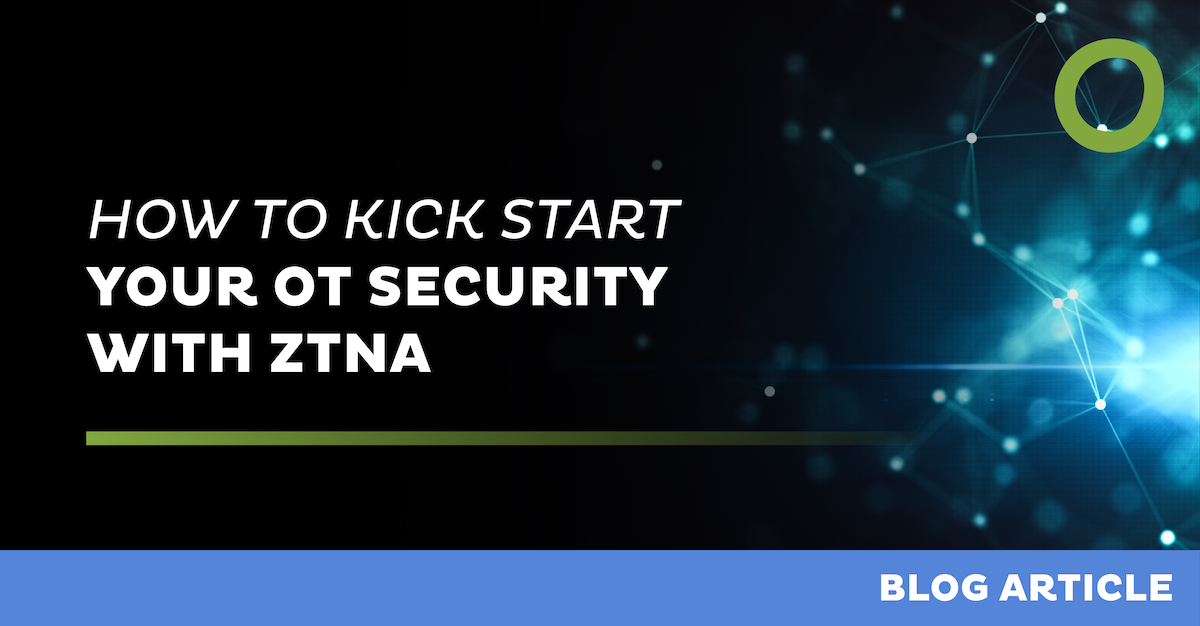
Securing Operational Technology (OT) environments has become a top priority for industrial organizations worldwide. While Information Technology (IT) security has been in the limelight for decades, the unique requirements and challenges of OT security are only now gaining broader recognition. This article explores why OT security needs a different approach, outlines a common six-step strategy, and then proposes a more efficient path to achieving rapid and meaningful protection—helping organizations align with Zero Trust principles and meet regulatory requirements like NIS2.
Introduction
What is OT and how does it differ from IT?
Operational Technology (OT) refers to the systems that control and monitor industrial operations. This includes equipment like programmable logic controllers (PLCs), supervisory control and data acquisition (SCADA) systems, industrial robots, and other specialized devices used in manufacturing, energy, utilities, and critical infrastructure. In contrast, Information Technology (IT) primarily handles data exchange, storage, and processing in office networks.
The primary difference lies in the objectives:
- IT systems focus on confidentiality, integrity, and availability of data.
- OT systems focus on physical processes, safety, and continuous operational availability.
Why is securing OT different from securing IT?
Several factors contribute to the distinct nature of OT security:
- Legacy systems: Many OT systems were designed decades ago without cybersecurity in mind.
- High availability requirements: Downtime in an OT environment can halt production lines or compromise safety.
- Proprietary protocols and hardware: Unlike modern IT, OT may use protocols that are not widely supported or understood by typical cybersecurity tools.
- Regulatory and safety implications: Compromise in OT can lead to physical harm, making security crucial from a human and environmental safety standpoint.
Challenges in OT Security
The complexity of industrial setups makes security challenging. Production lines often run continuously, so taking systems offline for updates or security assessments can be difficult or expensive. Furthermore, the heterogeneity of equipment—ranging from modern digital controllers to legacy analog systems—complicates integration and standardization.
Examples of OT Security Breaches
Industrial organizations have fallen victim to attacks such as ransomware, causing significant downtime. In 2019, a major aluminum producer was struck by a ransomware attack that disrupted factories across multiple countries. Another example is the 2021 ransomware incident on a global meat processing company, which halted production lines, leading to supply chain and financial repercussions. These incidents illustrate the real-world consequences of inadequate OT security.
Common Approach to OT Security
A typical roadmap to secure OT follows these six steps:
- Asset Discovery
Before any security measures can be implemented, organizations need to know what assets they have. This includes identifying every device, firmware, software, and network segment in the OT environment. It can be a labor-intensive process but is vital for comprehensive security planning. - Greenfield and Brownfield Blueprints
- Greenfield projects refer to new facilities or production lines built from scratch. Here, organizations can design networks with security in mind from the outset.
- Brownfield projects involve upgrading existing facilities. These have legacy constraints and require careful planning to integrate new security controls without disrupting ongoing operations.
- Assessing Solutions/Partners
Once organizations have a clear view of their assets and target architecture, they explore technology partners and solutions. This involves evaluating various security vendors, managed services, and in-house capabilities to create a cohesive security framework. - Proof of Concept (PoC) and Contracting
Potential solutions are tested in a controlled environment to validate efficacy and performance. If successful, contracts are signed, and rollout plans are finalized. - Greenfield Implementation
New plants or production lines immediately benefit from the latest security designs and technologies. Since these are newly built, they can adopt the blueprint without retrofitting older systems. - Brownfield Migration
Upgrading existing plants is typically slow and complex. Each upgrade must minimize downtime and ensure continuous operations, so this step often lags behind Greenfield deployments.
Why is this six-step approach common?
This methodical approach ensures that organizations have a complete inventory and plan before they invest in new solutions. It also respects the operational constraints of industrial environments, where abrupt changes can jeopardize production and safety.
A Better Approach with Important Quick Wins
While the six-step strategy is thorough, it has a significant downside: it takes a long time before the OT environment begins to see protective benefits. Asset discovery (Step 1) alone can span 6–9 months for large enterprises. Typically, it might take a year to move through Steps 1, 2, and 3, with another 6 months to start implementing changes in existing facilities (Step 6). The result is an 18-month window where vulnerabilities remain largely unaddressed.
What can be done during Step 1 to accelerate protection?
One impactful quick win is to deploy Zero Trust Network Access (ZTNA) solutions to secure remote access for partners and employees. In many industrial environments, remote maintenance and support services are exposed directly to the internet, creating glaring points of vulnerability. By implementing a ZTNA solution, organizations can close these exposed channels quickly.
Why is ZTNA so effective?
- Immediate risk reduction: When remote access isn’t left wide open, attackers have a much smaller attack surface to exploit.
- Incremental adoption: ZTNA can be deployed with minimal disruption to current OT operations. Often, you only need to add a dedicated gateway appliance or virtual gateway devices for redundancy.
- User-by-user migration: Rather than needing to overhaul the entire network, you can gradually onboard users to the new secure access method. This means less downtime and fewer integration issues.
Although introducing ZTNA doesn’t provide 100% coverage (since comprehensive asset discovery and segmentation are still necessary), it dramatically reduces the most obvious and easily exploitable security holes early on. Once remote access is secured, attackers require far more resources and “criminal energy” to penetrate the environment.
Summary
Securing OT environments is inherently complex. A careful, methodical approach—asset discovery, blueprinting, assessing solutions, PoC, and gradual rollout—ensures comprehensive protection. However, the downside is the long lead time before tangible security benefits take hold, leaving OT systems vulnerable to advanced threats.
By introducing ZTNA early in the process, organizations secure remote access channels, reducing the biggest risk factors right away. This aligns well with Zero Trust principles—never trust, always verify—and helps organizations move more confidently toward a robust OT security posture. It also contributes significantly to NIS2 compliance, as it demonstrates that you are actively protecting critical infrastructure from external threats and controlling who can access sensitive systems.
In today’s threat landscape, waiting a year or more to strengthen security can be disastrous. Combining the strategic depth of the traditional OT security roadmap with immediate, low-intrusion measures like ZTNA can transform how quickly and effectively you protect your industrial operations—and ultimately help ensure the safety and resilience of your organization.
Leave Complexity
Behind
To learn how Open Systems SASE Experience can benefit your organization, talk to a specialist today.
Contact Us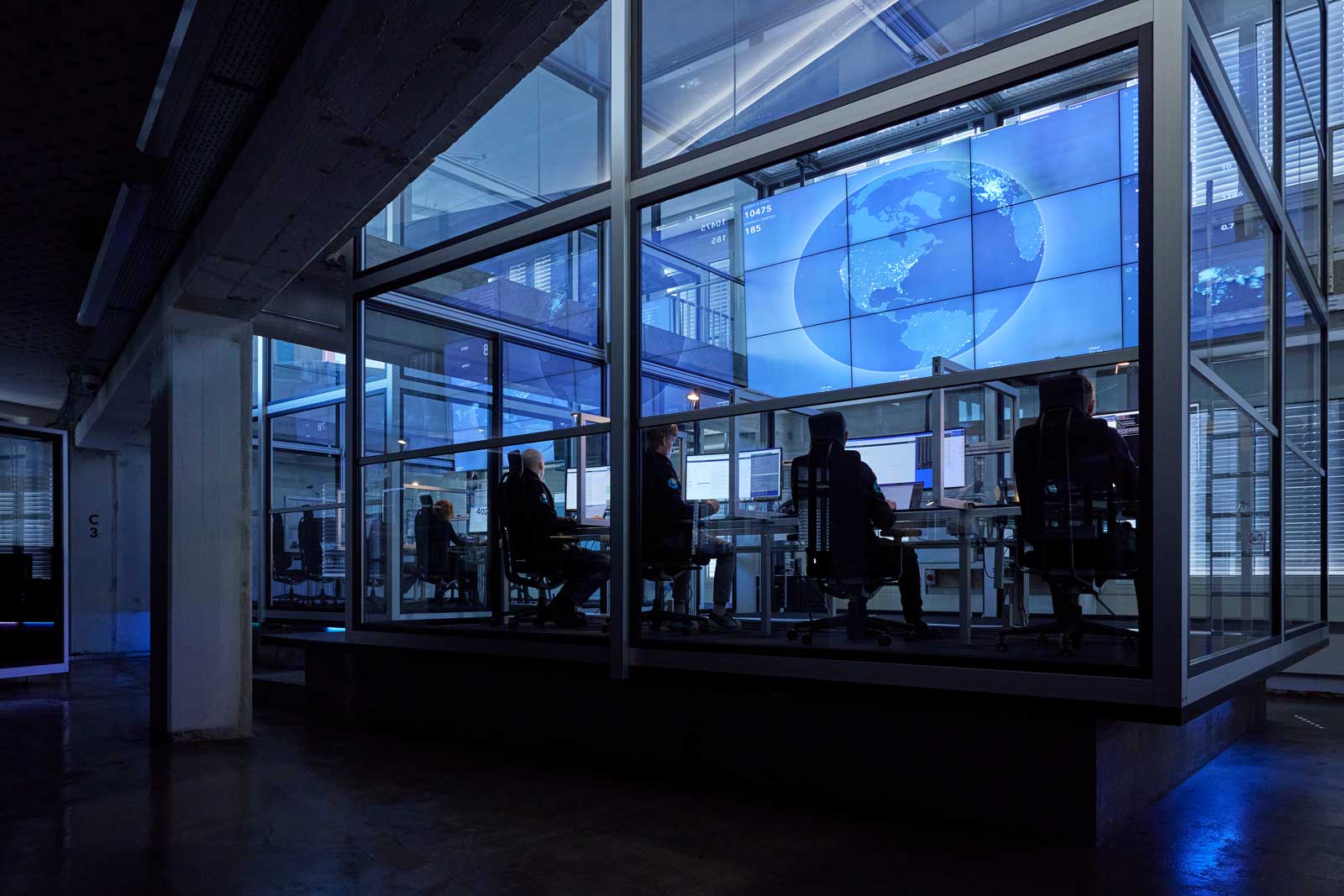